Concluding water tank tomfoolery:
After letting the paint dry and cure for a few days, the tops got a generous bead of sealer and I glued and screwed the tops down:
Tip o' the day: Check the date on your tube of LifeSeal BEFORE loading everything up and going to the boat. Assume that an unopened tube with a 2017 date has hardened in the tube
. Makes life easier to just assume that
.
Next up was to reinstall the floorboards (hopefully for the last time!) and reinstall the cabinetry for a final fitment check/adjustment before blowing it all back apart for clearcoat. But first - one last item:
I had been putting off deciding on starting batteries. I have been back and forth on this: one option is the starting battery should be the same type as the house batteries, in case a house battery fails. I've always wondered about this, because if a house battery fails and you replace it with the starting battery, how are you going to start the engine with a failed battery? If I were using golf cart batteries for the house bank, maybe, but since I'm going with Fireflys I just don't see it. I went with option two: I have two perfectly good batteries on hand - bought for the express purpose of powering the bilge pump while I was on the hard. The pragmatic Scotsman in me says why buy an additional $500+ battery when these will work just fine. With that decision made, time to build the battery box for the starting batteries. First up is to mock up the location:
Then build and mount the box:
And when satisfied, take it all apart, glue and screw it and seal it:
Next up, some cabinetry finish work!
Cheers,
Mark
After letting the paint dry and cure for a few days, the tops got a generous bead of sealer and I glued and screwed the tops down:
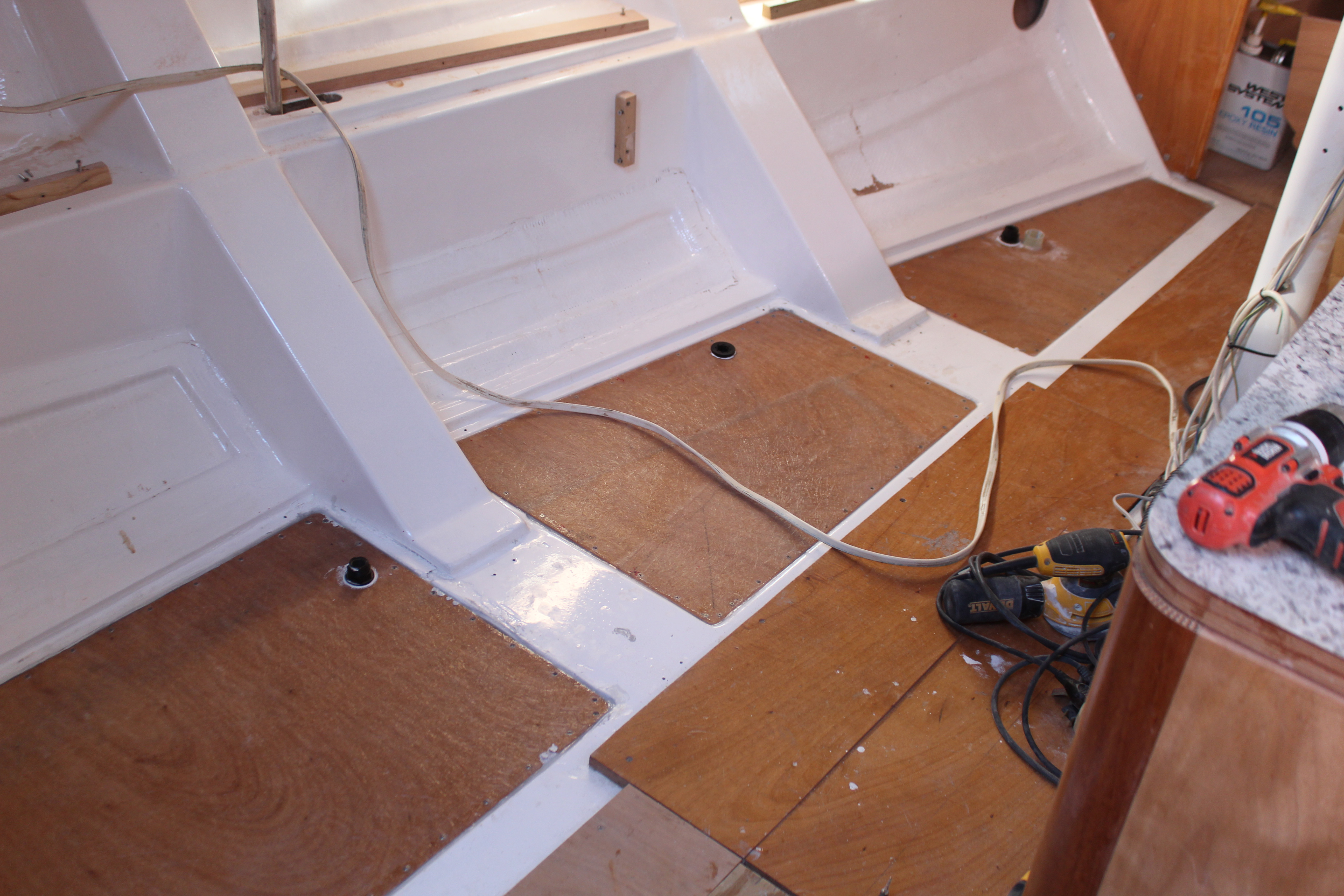
Tip o' the day: Check the date on your tube of LifeSeal BEFORE loading everything up and going to the boat. Assume that an unopened tube with a 2017 date has hardened in the tube
Next up was to reinstall the floorboards (hopefully for the last time!) and reinstall the cabinetry for a final fitment check/adjustment before blowing it all back apart for clearcoat. But first - one last item:
I had been putting off deciding on starting batteries. I have been back and forth on this: one option is the starting battery should be the same type as the house batteries, in case a house battery fails. I've always wondered about this, because if a house battery fails and you replace it with the starting battery, how are you going to start the engine with a failed battery? If I were using golf cart batteries for the house bank, maybe, but since I'm going with Fireflys I just don't see it. I went with option two: I have two perfectly good batteries on hand - bought for the express purpose of powering the bilge pump while I was on the hard. The pragmatic Scotsman in me says why buy an additional $500+ battery when these will work just fine. With that decision made, time to build the battery box for the starting batteries. First up is to mock up the location:
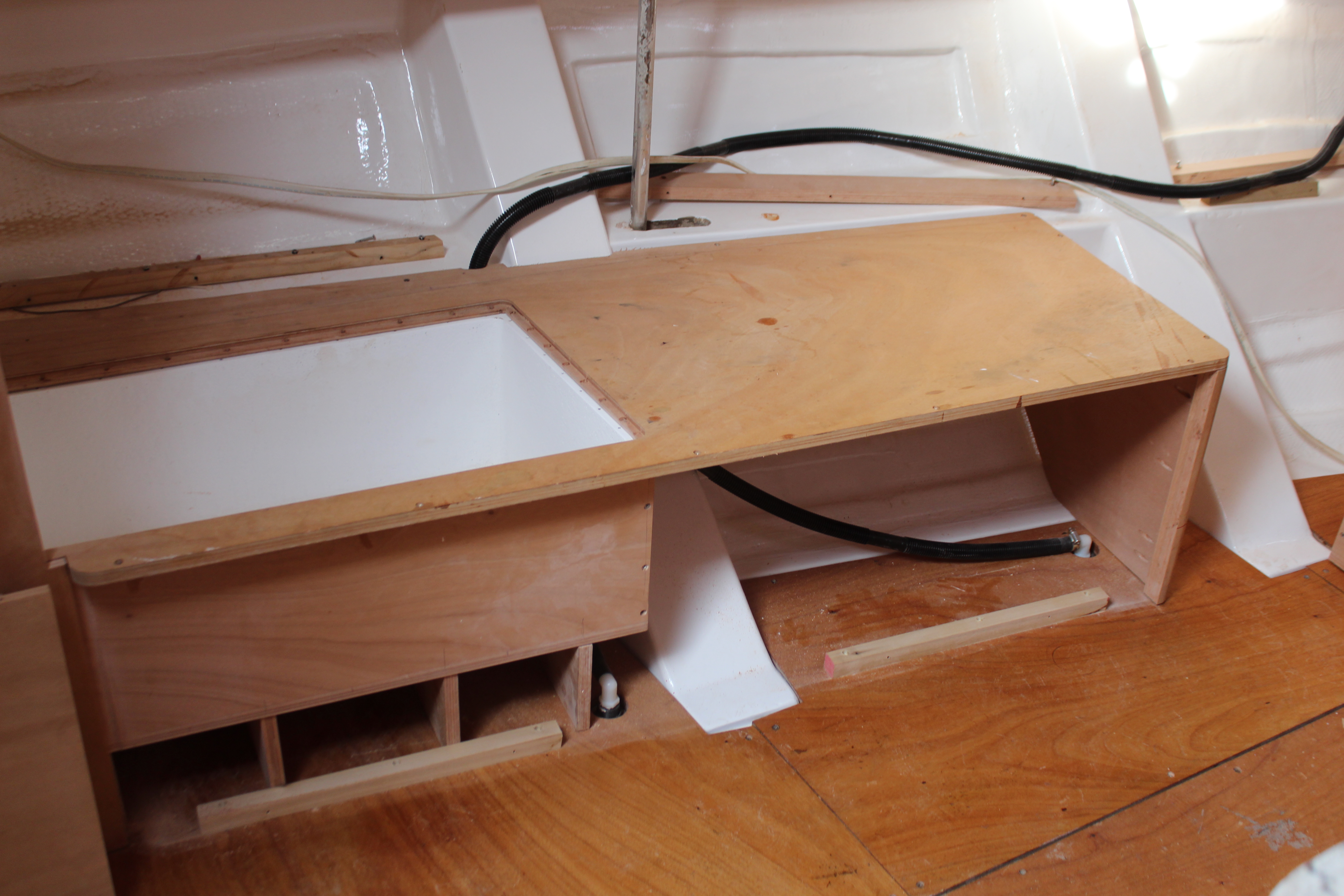
Then build and mount the box:

And when satisfied, take it all apart, glue and screw it and seal it:
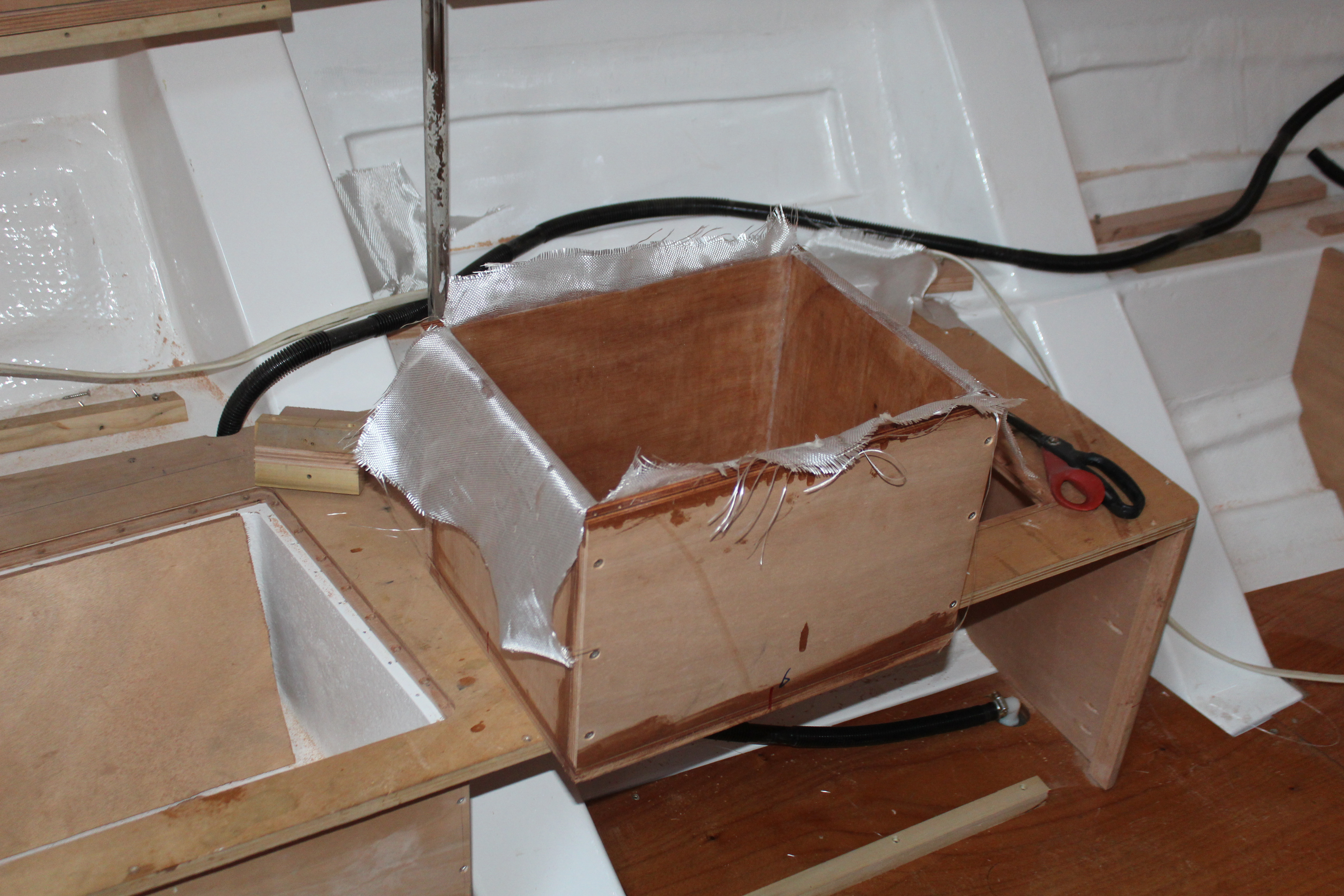
Next up, some cabinetry finish work!
Cheers,
Mark