What the heck is that..???
I am currently doing a shaft, cutlass, coupling and alignment job and when I arrived at my buddies shop the other day the job was not yet done. Cool.:cussing: Actually, it was cool because he allowed me to make a short video of how facing a coupling is actually done.
Here's the video: Facing A Marine Shaft Coupling (LINK)
Faced:
So what is "fitting & facing".
Fitting: To fit a straight or split coupling to the shaft for an interference fit. Good shops will usually strive for lighter than a bearing press fit but more than what you can slide on easily by hand.
Before you can face the coupling you first need to fit the new coupling to the new shaft or old shaft. Rusted old couplings can rarely, if ever, be re-used due to loss in tolerance from the layer of rust broken free during removal.
Sailboat couplings from reputable manufacturers such as Buck Algonquin & Walters usually always ship a little under sized so that they can be "fitted" to the shaft and not be loose. Even though it was a split coupling it still requires fitting and facing. My shafting shop is VERY picky. This fit is most always a light tap fit meaning you need often need to tap the coupling on with a wood or lead mallet.
The proper fit of the coupling to the shaft is critical, especially with straight couplings, but even with split couplings. If the fit is sloppy it will work the set screw holes, and the key, if the draw bolts come loose, and in a worst case a shaft can pull out of the coupling. A more likely scenario is that both become ruined from slop movement and in extreme cases the key works the shaft so much that it fails. This failure is often right at the end of the keyway. A loose prop can do the same.
Fitting is often done by hand with the aid of a machine shop lathe to hold the coupling. The reaming tool for this is very precise and they are quite expensive. It is used for the rough fitting. The coupling is most often inserted into the head of the lathe and the reaming tool end centered so the reamer goes in perfectly straight. The machinist makes a couple of turns of the reamer with a wrench and then removes the coupling and test fits it. This rough fit can usually be done in two or three tries. This one took three fittings. Care is taken to not to go to big because you can never make the hole smaller. Multiple fittings is usually the reality. This one took about 12-15 minutes to fit to the shaft.
Because this was a split coupling it was shimmed square to maintain the "fit" all the way through. The shimming was measured as accurately as possible before hand reaming.
The reamer is then adjusted by hand and inserted & centered into the coupling. It is then turned by hand with a wrench. After a couple of turns it is removed and the fit is checked. If not good this is repeated.
A good final fitting requires a lead mallet to tap the coupling onto the shaft.
Once it is fitted the coupling is installed on the shaft, with key or without, does not really matter, and with the set screws in place and is then ready for facing.
Facing: This makes the flange face rotate perfectly square to the shaft with no wobble.
Facing is rather easy compared to fitting and the video can be seen above. If you listen carefully you can hear the woo, wooo, wo as it is ground. The noise is not smooth because the cutting head was taking more in some areas and less in others due to wobble in the flange face.
Shaft flanges are aligned to roughly .001" for every inch of coupling diameter. Thus, a 4" coupling should be aligned to somewhere between .003" & .004". If the face is out .001" - .003" because it was not faced this can get inaccurate and a become a bear to align.
Gear box flanges are faced at the factory to spin true. Provided you have not bent it through pounding on it, or using it to press off a coupling, it should be darn close to rotating true. Unless your coupling is like new, with no rust between it and the shaft, I don't advise pressing the coupling off the shaft with it. Some gear boxes, like the small Hurth's (HBW-50 etc.), have very flimsy output shafts and they can easily fracture or be bent. It doe not take much to achieve a .003" or greater bend in a gear box coupling.
Often times with old shafts the easiest way to remove the coupling is to cut the shaft. This 1987 shaft had bad cutlass wear as well as bad stuffing box wear, and the coupling was not coming off in the boat any other way due to very limited access. A new shaft & coupling is far less costly than ruining your gear box!!
I am currently doing a shaft, cutlass, coupling and alignment job and when I arrived at my buddies shop the other day the job was not yet done. Cool.:cussing: Actually, it was cool because he allowed me to make a short video of how facing a coupling is actually done.
Here's the video: Facing A Marine Shaft Coupling (LINK)
Faced:
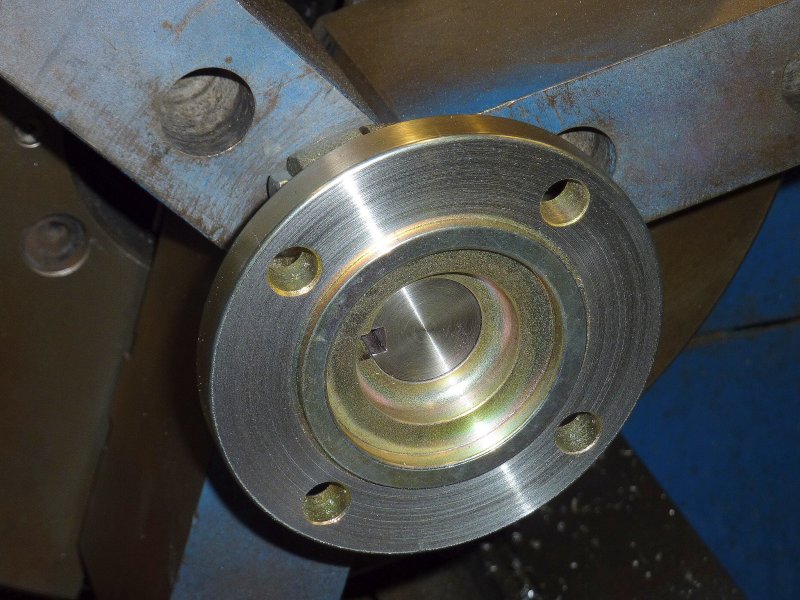
So what is "fitting & facing".
Fitting: To fit a straight or split coupling to the shaft for an interference fit. Good shops will usually strive for lighter than a bearing press fit but more than what you can slide on easily by hand.
Before you can face the coupling you first need to fit the new coupling to the new shaft or old shaft. Rusted old couplings can rarely, if ever, be re-used due to loss in tolerance from the layer of rust broken free during removal.
Sailboat couplings from reputable manufacturers such as Buck Algonquin & Walters usually always ship a little under sized so that they can be "fitted" to the shaft and not be loose. Even though it was a split coupling it still requires fitting and facing. My shafting shop is VERY picky. This fit is most always a light tap fit meaning you need often need to tap the coupling on with a wood or lead mallet.
The proper fit of the coupling to the shaft is critical, especially with straight couplings, but even with split couplings. If the fit is sloppy it will work the set screw holes, and the key, if the draw bolts come loose, and in a worst case a shaft can pull out of the coupling. A more likely scenario is that both become ruined from slop movement and in extreme cases the key works the shaft so much that it fails. This failure is often right at the end of the keyway. A loose prop can do the same.
Fitting is often done by hand with the aid of a machine shop lathe to hold the coupling. The reaming tool for this is very precise and they are quite expensive. It is used for the rough fitting. The coupling is most often inserted into the head of the lathe and the reaming tool end centered so the reamer goes in perfectly straight. The machinist makes a couple of turns of the reamer with a wrench and then removes the coupling and test fits it. This rough fit can usually be done in two or three tries. This one took three fittings. Care is taken to not to go to big because you can never make the hole smaller. Multiple fittings is usually the reality. This one took about 12-15 minutes to fit to the shaft.
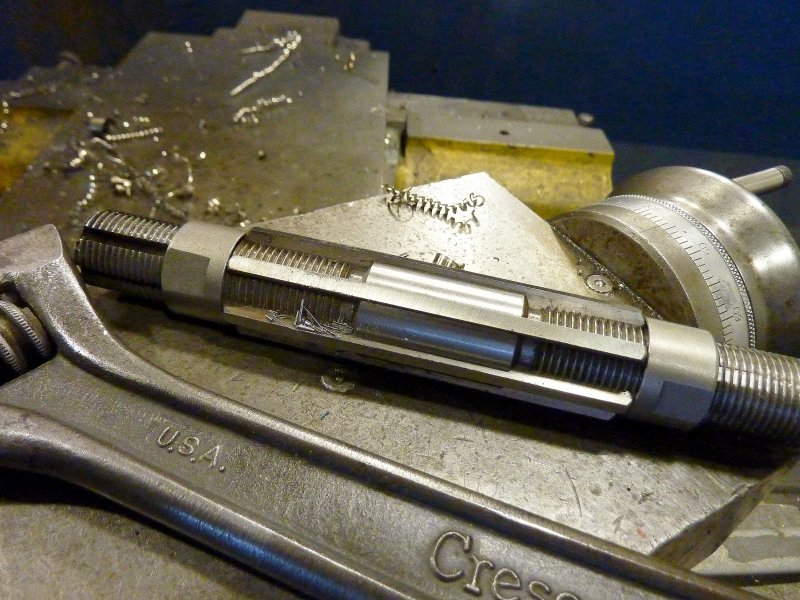
Because this was a split coupling it was shimmed square to maintain the "fit" all the way through. The shimming was measured as accurately as possible before hand reaming.
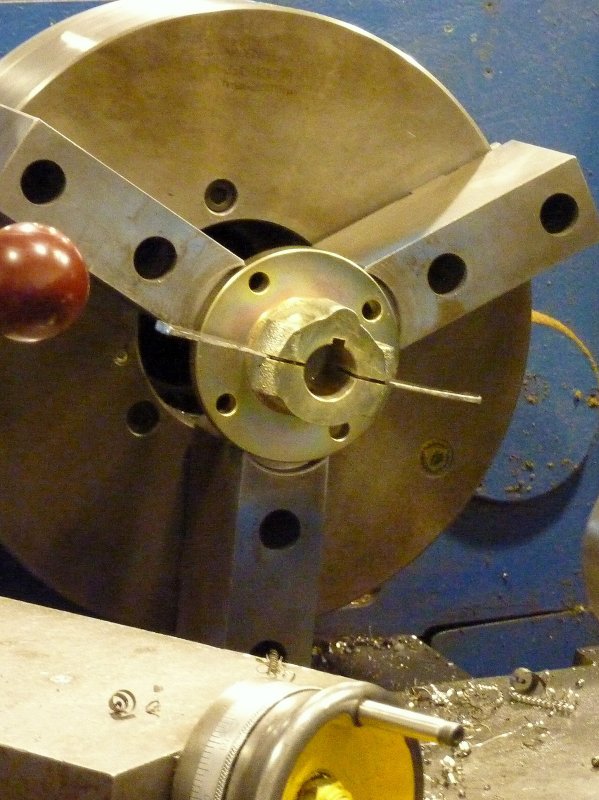
The reamer is then adjusted by hand and inserted & centered into the coupling. It is then turned by hand with a wrench. After a couple of turns it is removed and the fit is checked. If not good this is repeated.
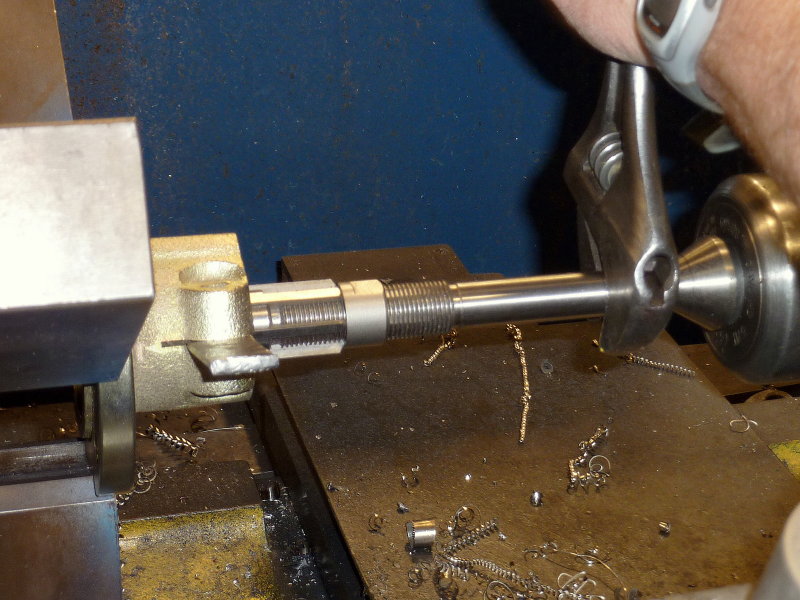
A good final fitting requires a lead mallet to tap the coupling onto the shaft.
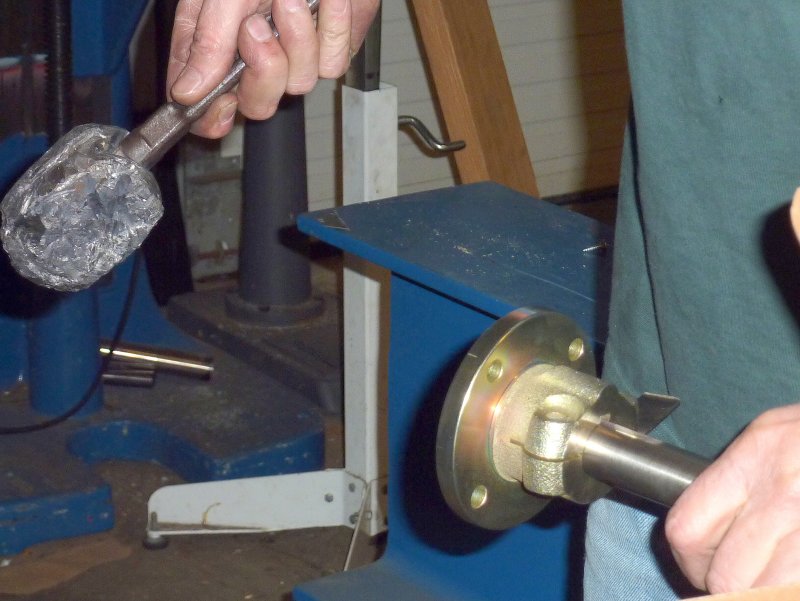
Once it is fitted the coupling is installed on the shaft, with key or without, does not really matter, and with the set screws in place and is then ready for facing.
Facing: This makes the flange face rotate perfectly square to the shaft with no wobble.
Facing is rather easy compared to fitting and the video can be seen above. If you listen carefully you can hear the woo, wooo, wo as it is ground. The noise is not smooth because the cutting head was taking more in some areas and less in others due to wobble in the flange face.
Shaft flanges are aligned to roughly .001" for every inch of coupling diameter. Thus, a 4" coupling should be aligned to somewhere between .003" & .004". If the face is out .001" - .003" because it was not faced this can get inaccurate and a become a bear to align.
Gear box flanges are faced at the factory to spin true. Provided you have not bent it through pounding on it, or using it to press off a coupling, it should be darn close to rotating true. Unless your coupling is like new, with no rust between it and the shaft, I don't advise pressing the coupling off the shaft with it. Some gear boxes, like the small Hurth's (HBW-50 etc.), have very flimsy output shafts and they can easily fracture or be bent. It doe not take much to achieve a .003" or greater bend in a gear box coupling.
Often times with old shafts the easiest way to remove the coupling is to cut the shaft. This 1987 shaft had bad cutlass wear as well as bad stuffing box wear, and the coupling was not coming off in the boat any other way due to very limited access. A new shaft & coupling is far less costly than ruining your gear box!!
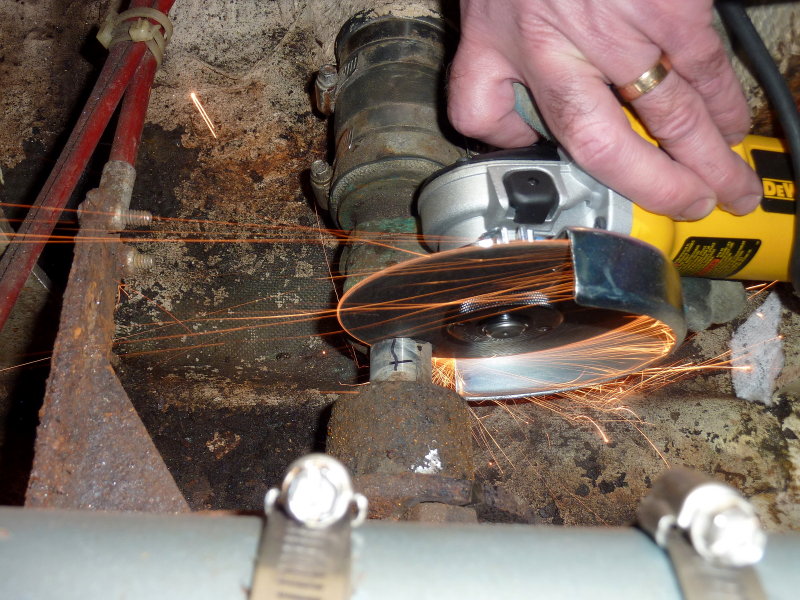