I am planning on building new hatch boards from milled 1/2" or 5/8" mahogany. My inclination is to build them with a vertical grain direction so wood movement would minimize warping. The plan would be to treat all end grain and long grain with epoxy and then varnish.
So many hatch boards I see are built with horizontal grain direction so I thought I would ask the groups opinion on grain orientation.
I am also looking for any opinions/advise/weblinks for building ventilation louvers into the hatch boards. I am currently leaning towards cutting the boards, angle routing the vents and then re-gluing the pieces. I have attached a diagram for reference. Any thoughts?
Thanks for any replies....a
So many hatch boards I see are built with horizontal grain direction so I thought I would ask the groups opinion on grain orientation.
I am also looking for any opinions/advise/weblinks for building ventilation louvers into the hatch boards. I am currently leaning towards cutting the boards, angle routing the vents and then re-gluing the pieces. I have attached a diagram for reference. Any thoughts?
Thanks for any replies....a
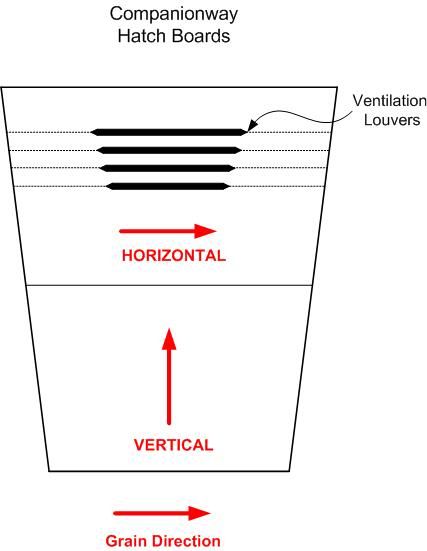